Unlocking the Power of Compressed Air Driven Vacuum Pumps

In today's fast-paced industrial landscape, efficiency and reliability are paramount. One technology that plays a crucial role in achieving these goals is the compressed air driven vacuum pump. These ingenious devices harness the power of compressed air to create a vacuum, offering a range of advantages in diverse applications.
Imagine a system that can effortlessly lift, hold, and move materials, all without the need for complex electrical connections. That's the essence of a compressed air vacuum pump. By using readily available compressed air as a power source, these pumps provide a safe, reliable, and cost-effective solution for various vacuum needs. From packaging and printing to material handling and automation, compressed air vacuum pumps have become indispensable tools.
The principle behind these pumps is remarkably simple yet effective. Compressed air flows through a specially designed venturi, creating a low-pressure area that draws in surrounding air. This creates suction, effectively generating a vacuum. The simplicity of the design contributes to the robustness and longevity of these pumps, minimizing maintenance requirements and maximizing uptime.
While the exact origins of the compressed-air-powered vacuum generator are difficult to pinpoint precisely, its development is intertwined with the broader history of pneumatic technology. As understanding of the properties of compressed air and its potential applications grew, innovations like the venturi effect paved the way for the creation of air-driven vacuum pumps. These pumps quickly gained popularity in industries where safety, reliability, and ease of use were paramount.
A key advantage of these pumps is their intrinsic safety. Unlike electrically powered vacuum pumps, they pose no risk of sparks or electrical hazards, making them ideal for use in flammable or explosive environments. This feature makes them indispensable in industries like chemical processing, pharmaceuticals, and mining. Furthermore, the absence of electrical components reduces the risk of malfunctions and downtime.
Compressed air driven vacuum systems offer several benefits. Firstly, they are inherently safe due to their non-electrical operation, reducing fire risks. For instance, in chemical plants, they are used to handle flammable liquids. Secondly, their simplicity translates to easy maintenance and lower costs compared to electric pumps. An example is their use in automated packaging lines where minimal downtime is crucial. Thirdly, their portability, due to reliance on compressed air lines, makes them ideal for applications like robotics and material handling in diverse locations within a factory.
When choosing a compressed-air vacuum pump, consider factors like required vacuum level, airflow rate, and the availability of compressed air. Ensure your system has adequate air pressure and flow capacity to power the pump effectively.
One real-world example involves using compressed air vacuum pumps in a printing facility to lift and position large paper sheets. Another application is in automated assembly lines, where they pick and place small components. In the food industry, they are employed for packaging delicate products like baked goods, preventing damage. In laboratories, these pumps provide a safe and reliable vacuum source for filtration and other processes.
Advantages and Disadvantages of Compressed Air Driven Vacuum Pumps
Advantages | Disadvantages |
---|---|
Safe in hazardous environments | Dependent on a compressed air supply |
Simple operation and maintenance | Can be noisy |
Portable and easy to install | Less efficient than some electric pumps for high vacuum levels |
One common challenge is insufficient compressed air supply, resulting in reduced vacuum performance. The solution is to ensure the air compressor system can meet the pump's demands. Another issue is noise, which can be mitigated with silencers or mufflers.
Frequently Asked Questions:
1. What is a compressed air driven vacuum pump? - A pump that uses compressed air to generate vacuum.
2. Are they safe in flammable environments? - Yes, due to their non-electrical operation.
3. How do they work? - Compressed air passes through a venturi, creating suction.
4. What are their main applications? - Material handling, packaging, printing, etc.
5. How do they compare to electric vacuum pumps? - Safer in hazardous environments but potentially less efficient for high vacuum levels.
6. How do I choose the right pump? - Consider required vacuum level, airflow, and air supply.
7. What are some common troubleshooting tips? - Check for leaks, ensure adequate air supply, and clean/replace filters.
8. What is the typical lifespan of these pumps? - With proper maintenance, they can last for many years.
Tips and tricks for maximizing performance include regular cleaning of filters, checking for leaks, and ensuring a consistent compressed air supply.
In conclusion, compressed air driven vacuum pumps offer a robust and versatile solution for a wide range of industrial applications. Their inherent safety, simplicity, and ease of maintenance make them valuable tools in various settings. From automating manufacturing processes to ensuring safety in hazardous environments, these pumps play a critical role in enhancing efficiency and reliability. By understanding their operating principles, benefits, and best practices, businesses can leverage the power of compressed air vacuum pumps to optimize their operations and achieve their goals. The future of compressed air driven vacuum pumps looks bright, with ongoing research and development focused on improving efficiency and expanding their applications. As industries continue to prioritize safety, reliability, and cost-effectiveness, these versatile pumps are poised to play an even greater role in shaping the industrial landscape of tomorrow. Exploring their capabilities is a crucial step for any business seeking innovative solutions for their vacuum needs.
Kansas city weather insights two week outlook
Stella artois mini keg your guide to draught perfection
Unmasking afton the many faces of william afton











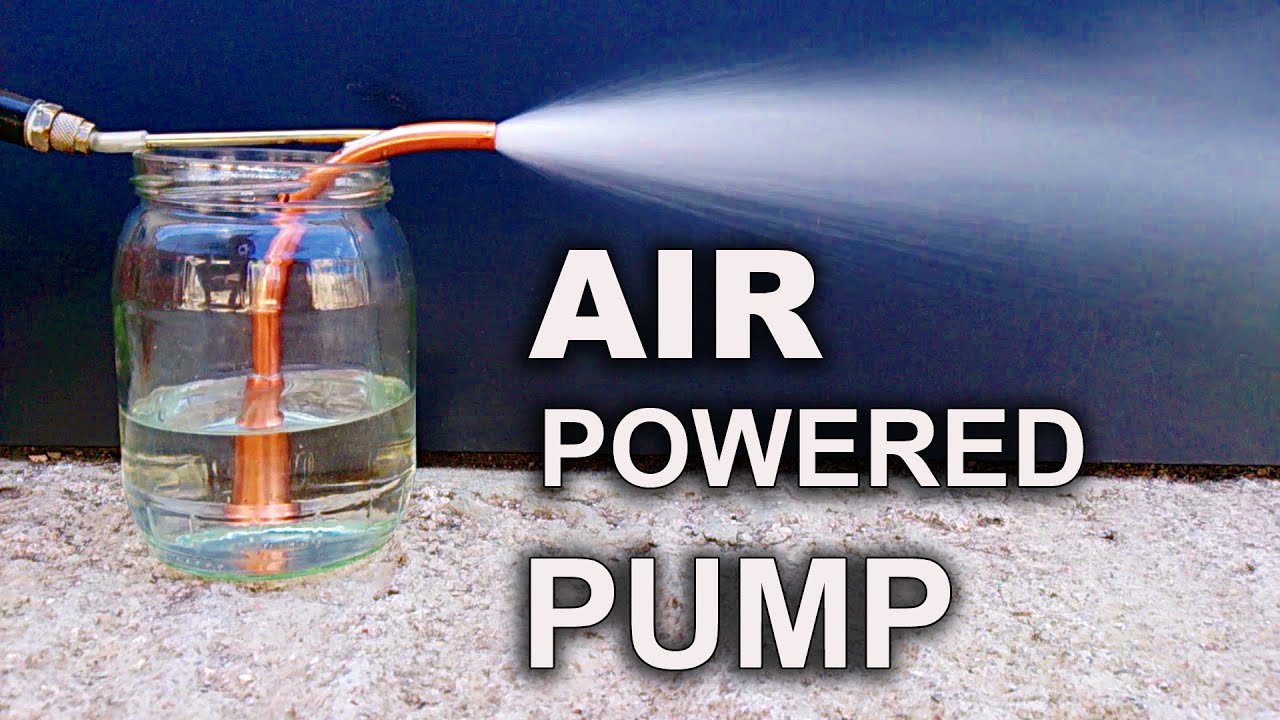
