Decoding the Level Switch Low Low Symbol Mystery
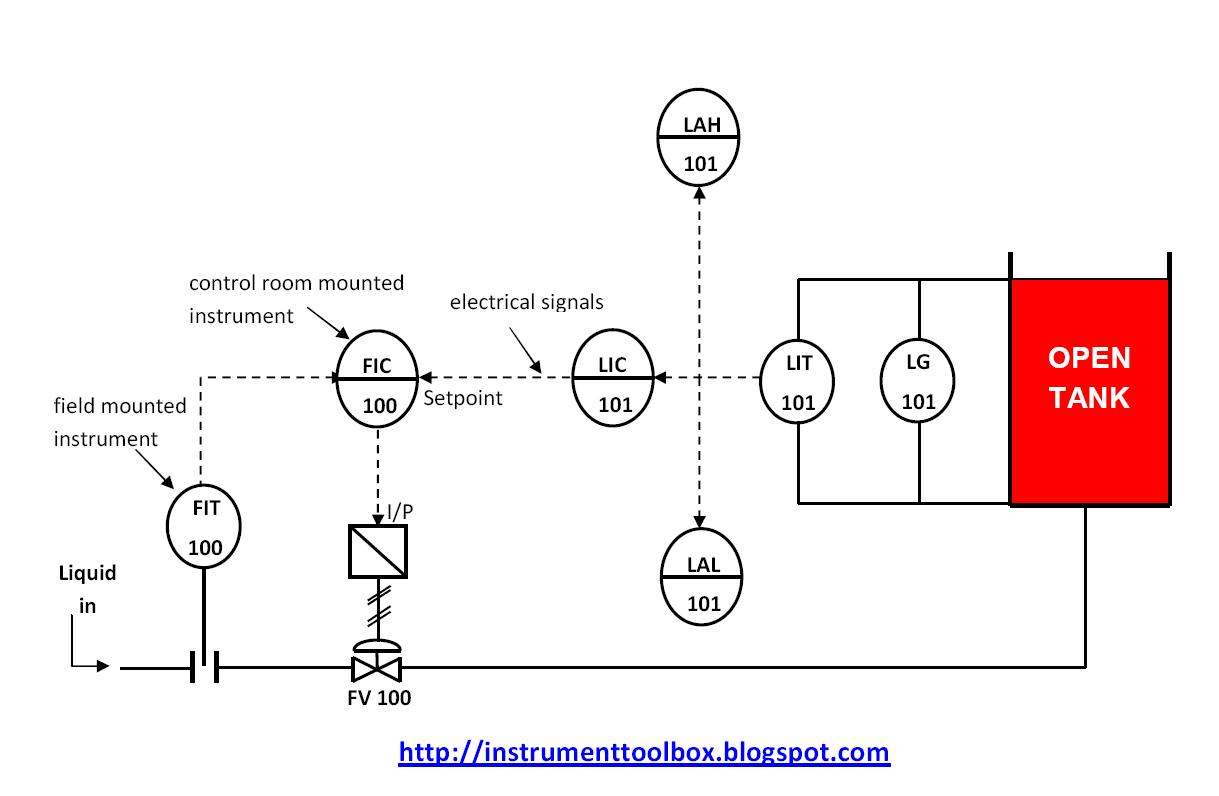
Imagine a silent sentinel, tirelessly monitoring the depths of a tank, ensuring a critical process flows smoothly. This unsung hero is the level switch, and its "low low" symbol often holds the key to preventing costly spills, equipment damage, or process interruptions. But what exactly does this cryptic symbol signify, and why is it so crucial in the world of industrial automation?
The "level switch low low symbol" represents a critical threshold in tank or container level monitoring. It signifies that the material being measured has fallen to a critically low point, often well below the normal operating range. This indicator triggers an alarm or automated response to prevent potentially disastrous consequences. Understanding the nuances of this symbol and its associated circuitry is essential for anyone working with level measurement and control systems.
The history of level switching mechanisms dates back to the earliest days of industrialization, evolving from simple float-based systems to sophisticated electronic sensors. The need to reliably detect low levels, particularly "low low" conditions, emerged as processes became more complex and the consequences of failure more severe. This led to the development of specialized symbols and standardized alarm systems to ensure rapid response to critical level drops.
The importance of the level switch low low symbol cannot be overstated. It serves as the last line of defense against potentially catastrophic events. In industries like chemical processing, oil and gas, and water treatment, a "low low" condition can indicate pump cavitation, material shortages, or even dangerous leaks. The timely detection afforded by this symbol allows operators to intervene and prevent costly downtime, environmental damage, or safety hazards.
Issues related to a malfunctioning low-low level switch can be multifaceted. False alarms can lead to unnecessary shutdowns and wasted resources, while a failure to trigger an alarm in a genuine low-low scenario can have severe consequences. Understanding potential failure modes, such as sensor fouling, wiring issues, or calibration errors, is essential for maintaining a reliable and effective level control system.
A level switch low-low condition triggers specific actions based on the system's configuration. These actions might include activating backup pumps, shutting down processes, or sending alerts to maintenance personnel. A simple example would be a sump pump system where a low-low level triggers an alarm to prevent the pump from running dry and burning out.
Three key benefits of incorporating a low-low level switch include preventing equipment damage (e.g., pump burnout), ensuring process continuity by preventing material shortages, and enhancing safety by preventing hazardous spills or leaks. For instance, in a chemical processing plant, a low-low level switch in a reactor vessel can prevent a runaway reaction by automatically adding more reactants.
Advantages and Disadvantages of Level Switch Low Low Functionality
Advantages | Disadvantages |
---|---|
Prevents equipment damage | Potential for false alarms |
Ensures process continuity | Requires regular calibration and maintenance |
Enhances safety | Can be susceptible to sensor fouling |
Best practices for implementing low-low level switches include regular calibration, proper sensor placement to avoid dead zones, routine inspection for fouling or damage, redundant systems for critical applications, and comprehensive operator training.
Frequently Asked Questions:
1. What is a level switch low low symbol? - It indicates a critically low level in a tank or container.
2. Why is it important? - It prevents equipment damage, process interruptions, and safety hazards.
3. What causes false alarms? - Sensor fouling, wiring issues, or calibration errors.
4. How to troubleshoot a malfunctioning switch? - Check wiring, sensor condition, and calibration.
5. What are the different types of level switches? - Float switches, capacitive switches, ultrasonic sensors, etc.
6. How often should a level switch be calibrated? - Depends on the application and manufacturer recommendations, typically annually or semi-annually.
7. What are the consequences of ignoring a low-low alarm? - Equipment damage, process shutdown, potential safety hazards.
8. How can I improve the reliability of my level switch system? - Implement redundancy, regular maintenance, and proper sensor selection.
Tips and tricks related to level switches include understanding the specific requirements of your application, choosing the right type of switch for the material being measured, and ensuring proper installation and maintenance.
In conclusion, the level switch low low symbol represents a crucial safety net in various industrial processes. Its function goes beyond simple level detection; it acts as a critical safeguard against potentially disastrous events. By understanding its significance, implementing best practices, and addressing potential challenges, industries can ensure the smooth and safe operation of their processes, prevent costly downtime, and protect their valuable assets. Don't underestimate the power of this small symbol – it can make all the difference between smooth operation and a critical failure. Properly integrating and maintaining these systems is an investment in operational efficiency, safety, and ultimately, peace of mind. Take the time to understand the specifics of your system and ensure it's configured to meet your specific needs. This proactive approach can save you time, money, and potential headaches down the line. The relatively small investment in a robust and reliable level switching system pales in comparison to the potential costs of ignoring this crucial aspect of process control.
Transforming metal surfaces with johnstones smooth metal paint
Accessing private facebook profiles myths and realities
Unlocking the secrets of top tier medicare part b coverage








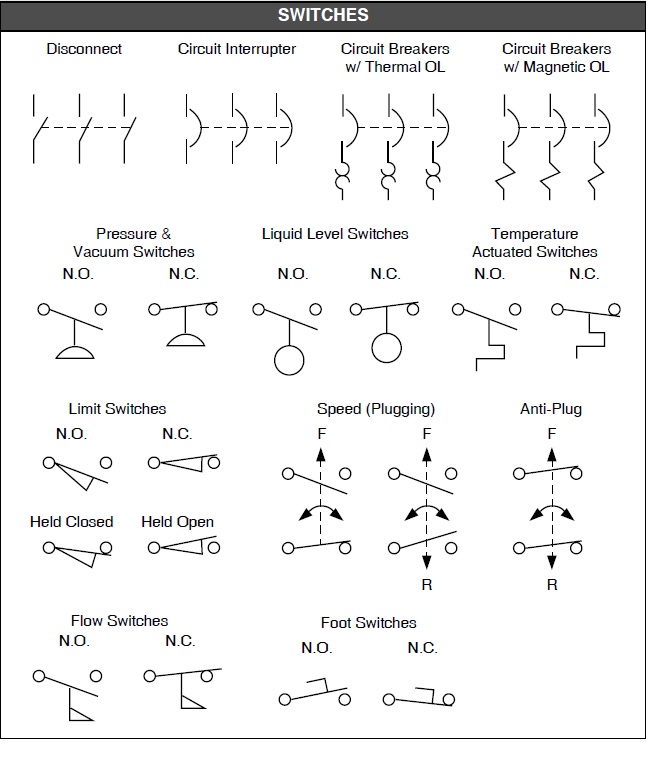

